How Soft Drinks are Made?
The recipe for soft drink is relatively simple, making them easy for production both at home and in large manufacturing facilities that can create millions of bottles of drink each week. However, even though all the ingredients can be easily found and mixed together during very straightforward manufacturing process, the end result can have very varying taste, feel and look that depends from the impurities that can be found in the ingredients (mostly water that represents up to 93% of a soft drink and sugar that can take 7-12% ratio).
Modern manufacturing process of carbonated soft drinks:
-
Water is a foundation of every soft drink, so much care needs to be taken for it to be cleaned from any impurities (organic matter, suspended particles and
bacteria) and stabilized to the desired pH level. Their removal is done through the series of processes such as boiling, coagulation, filtration and
chlorination.
-
Most successful filtration process is done via sand. Water goes through layer of sand and beads that catches foreign particles.
-
Sterilization is most often done with chlorine that is later removed with activated carbon filter (it also catches remaining organic matter that was not
caught by sand filter).
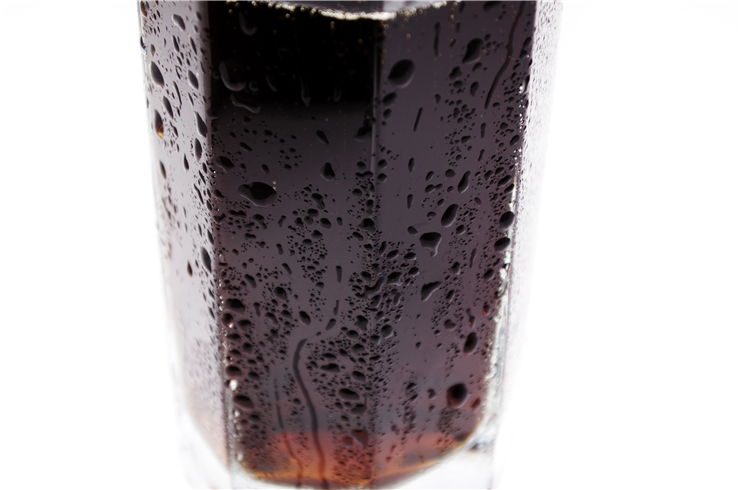
-
The main ingredients of the soft drink are introduced to the water tanks – sugar and flavor concentrates (which can be either in the form of powder or
syrup). To make resulting mix perfectly sterilized (some bacteria could be present in sugar/flavor ingredients), water tanks are either sterilized with
ultraviolet radiation or flash pasteurization (quick heating and cooling of water).
-
During entire process of mixing, it is highly recommended if the liquid is not allowed to absorb air. Because of that, some manufacturers are mixing their
ingredients inside chambers that are pressurized with carbon dioxide.
-
Finally at the very end of manufacture process, the water mixture is carbonized. Carbonization needs to be performed with exact cold temperature of liquid.
-
Packaging needs to be done very quickly, with containers that are immediately sealed so that carbon pressure in liquid could be preserved.
-
Labeling and packaging can then be applied, but most manufacturers wait for bottles to acclimate to room temperature so that they can avoid the
condensation of moisture on cold bottles.